Robotic Gripper for Automated Injection Molding
Developed as part of my graduate research, this custom robotic gripper system automates material handling for an injection molding process, enhancing overall efficiency.
Key Contributions & Features:
- Designed and manufactured the complete gripper structure.
- Wired and plumbed the pneumatic actuators for gripping actions.
- Programmed the Yaskawa industrial robot for coordinated movement and gripper control.
- Engineered a dual-sided end-effector to handle pre-forms (aluminum bushings, composite tape) and finished parts simultaneously.
- Key Benefit: Parallel operation (part removal + pre-form loading) significantly reduces machine cycle time.
Figure 1 shows the CAD design, illustrating the dual-sided approach. Figure 2 shows the gripper installed on the robot.
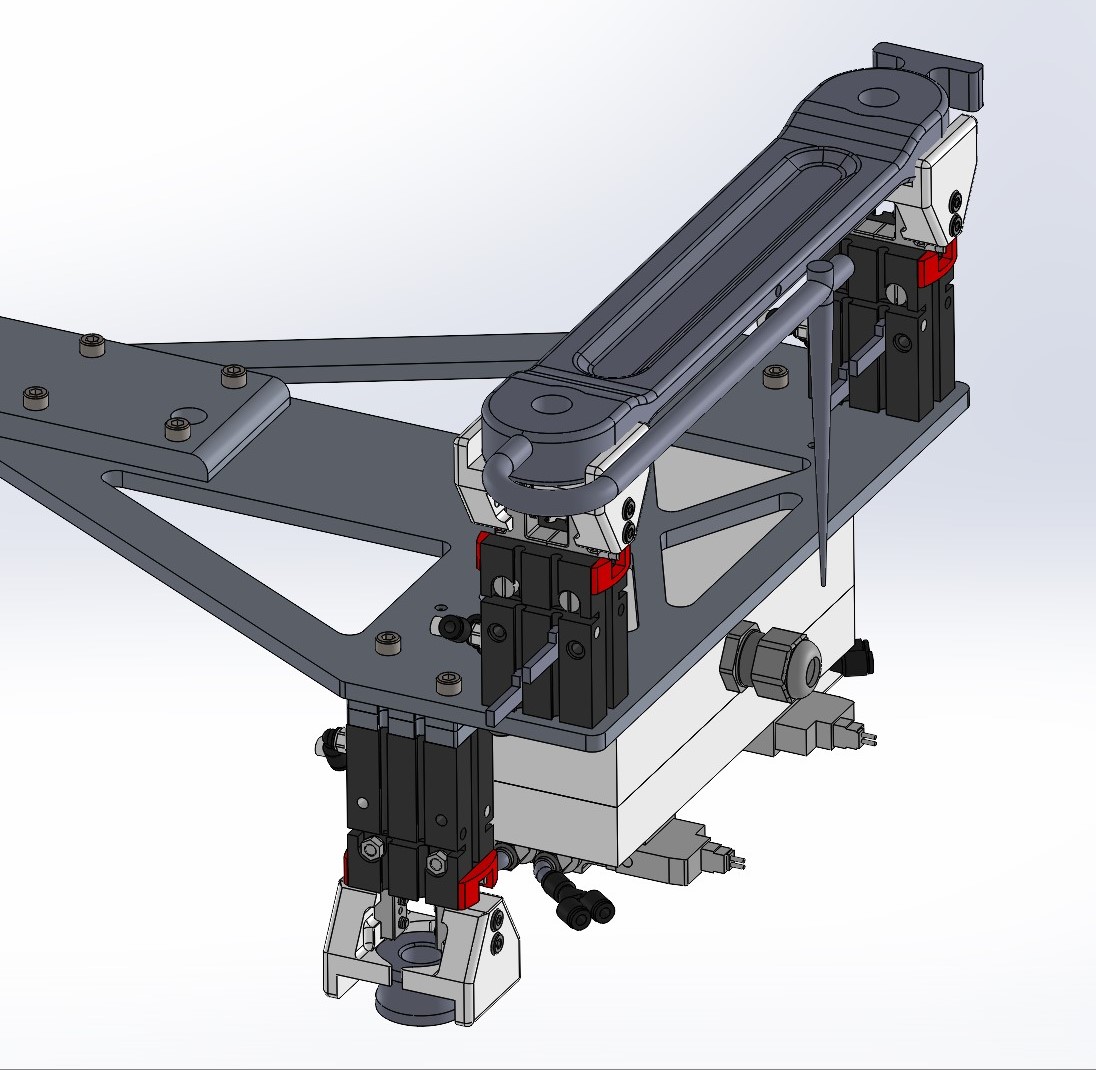
Figure 1: Robotic Gripper CAD
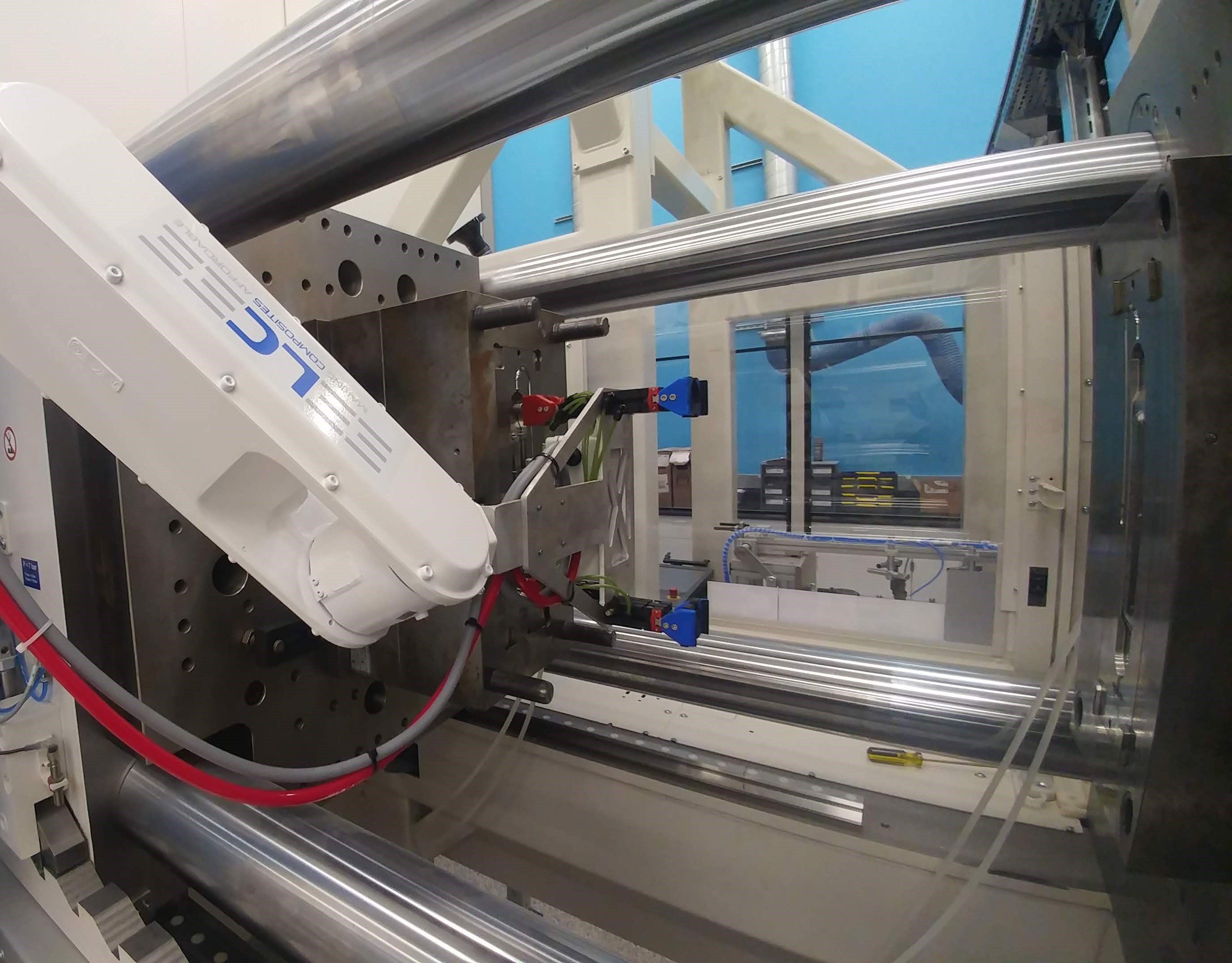
Figure 2: Robotic Gripper in-action
System Demonstration
The video below (Figure 3) demonstrates the robotic gripper system operating during a beta test phase, showcasing the automated loading and unloading sequence.
Figure 3: Video Demonstration of Gripper Operation (Beta Test)